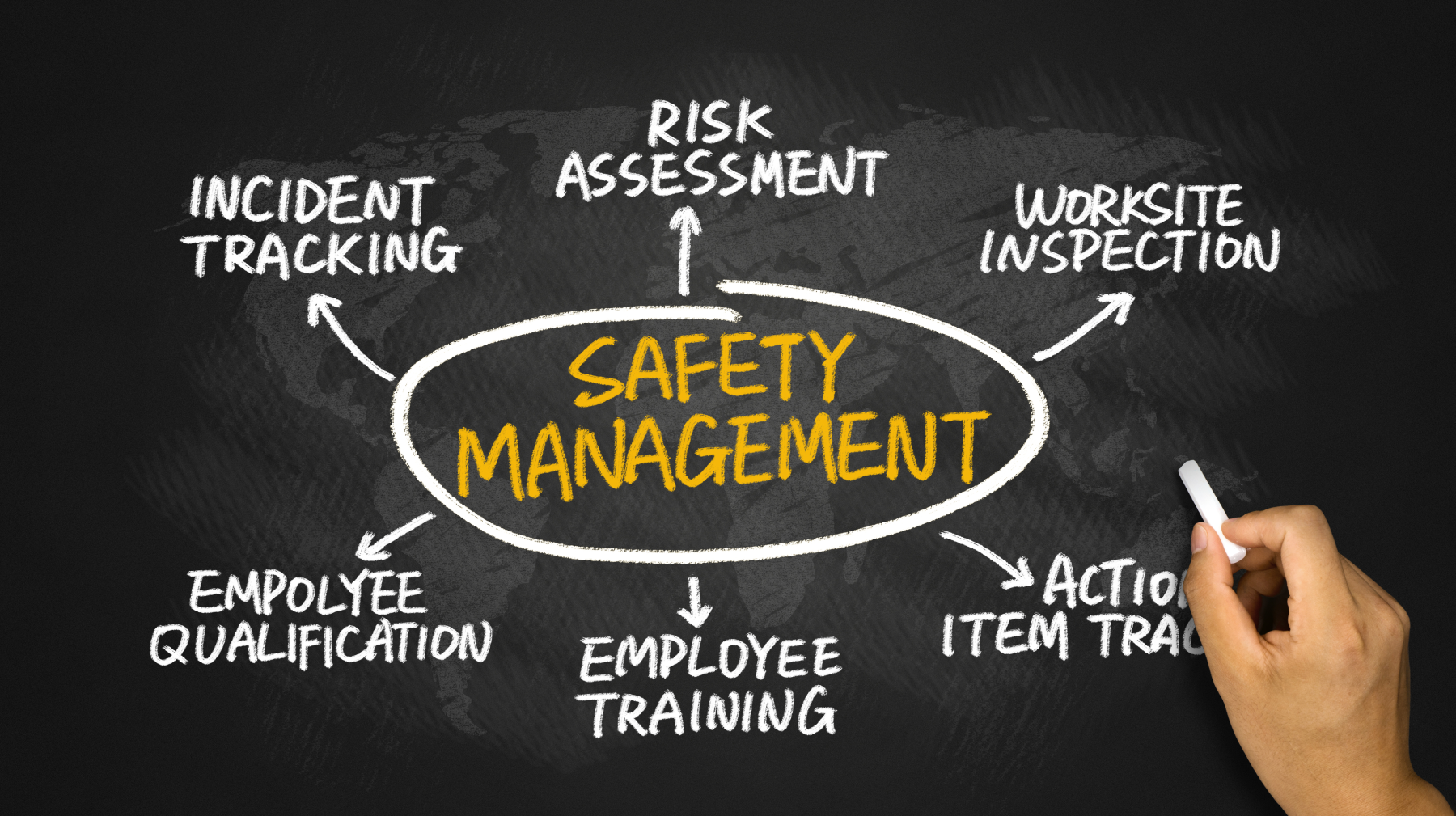
SAFETY FIRST, SAFETY ALWAYS
Make Risk Management a Part of Your Shop’s Culture (PAGE 8-11)
by Ben Cox
Risk management is an integral part of a successful business. Business owners and leaders must internalize that philosophy to achieve maximum return on their investment. Prioritizing safety — from senior management to front-line employees — helps protect employees. It also helps avoid errors that could dent or break the bottom line, and damage business in ways that are difficult, or even impossible, to come back from.
A shift in mindset is the first step. Turn your risk management program into a risk management culture.
“A program can feel like an extra burden to employees, while a culture feels natural,” said Federated Mutual Insurance Company Risk Consultant Chris Backlund.
WHAT’S AT STAKE?
Every injury, every lawsuit, every poor hire, every missed opportunity to plan hurts business. Insurance helps pay for the direct costs of a loss, such as property damage, medical bills, and legal expenses. But a business is responsible for the hidden expenses — hiring and training new employees, lost productivity, low morale, and potentially higher insurance premiums.
Don’t forget about one of a business’ most important assets: its reputation. A business is able to open its doors every day and fill orders because its leaders and employees have demonstrated a history of being reliable to potential and existing customers and employees.
It’s not hard to imagine a scenario in which a business’ hard-earned reputation disappears. An employee
who is improperly trained or not following safety protocols could make a costly mistake, injuring him or herself or putting an indispensable piece of equipment out of commission. Just like that, there’s an insurance claim (and possibly a lawsuit), and a business cannot fulfill its obligations to its customers.
The spiral continues. Employees, who need to trust that they are working in a safe environment, could begin to look for employment elsewhere. And clients, who depend on the products a business supplies them, could find new vendors, leading to a diminished book of business and a damaged bottom line.
HIGH-PERFORMING TEAM
While keeping the shop floor clear of hazards is a significant piece of any good risk management plan, building a high- performing team is also crucial to creating and maintaining a safe environment.
“Safety starts with who you hire,” said Federated Insurance Senior Risk Consultant Scott Grischow.
Reliable employees with records of working safely are key. Finding a committed and enthusiastic safety manager also helps create an effective risk management culture. Buy-in from all levels of management is equally vital.
“You need to find someone who truly believes safety is important,” Grischow said. “If your leaders are not excited about safety, your employees aren’t going to be excited. They take cues from you.”
GROUP EFFORT
With a team of high-performing, safety-conscious employees, businesses can operate at or near peak efficiency. Everything flows from there, including a commitment to safety. Walk throughs and regular audits can do wonders for a risk management program’s overall effectiveness, but what about the hazards that arise from every-day activities?
- On a busy manufacturing floor, hazards can be anywhere — so, the more eyes looking for them, the better. Don’t rely only on management to look out for workers’ safety. During meetings and training sessions, encourage everyone to say something if they see something unsafe.
- Periodically review the procedures for reporting incidents and injuries with employees. Keep the pressure low to avoid intimidating workers, but stress the importance of staying vigilant for potentially dangerous situations.
- Consider encouraging participation in a risk management culture by recognizing and rewarding incident reporting. Monetary or material rewards are common to show appreciation for workers’ attention to safety. But, craft the incentive program in a way that doesn’t discourage employees from reporting injuries for the sake of earning the incentive. The OSHA rule on incentivizing safety can be complicated, but its intent is to promote incident reporting. Research the regulation and consider consulting legal counsel if you are thinking about implementing such an approach.
GETTING STARTED
A good first contact is an insurance provider. Some insurance companies employ consultants whose sole purpose is to help policyholders identify and remove worksite hazards. Taking advantage of the opportunity to have facilities toured and reviewed by one of these professionals can provide a strong start.
An independent contractor can also provide an evaluation and give you some direction.
Whichever route you take, gaining extra perspectives can help you keep your business and employees safe, ensure compliance, and strengthen your commitment to safety.
CUSTOMIZED APPROACH
No two businesses are the same, so it’s important to understand that one size never fits all when it comes to risk management strategies. Even among similar operations within an industry, safety needs change from business to business.
“You need to analyze the work that you’re doing,” Grischow said. “Then you work down into the specifics.”
Fulfill the basic regulatory requirements first, then examine deeper needs. Think creatively and do research. Is fine oil mist a hazard? Consider equipment that removes the substance from the air before it has a chance to settle on walking surfaces, causing slip- and-fall accidents. Are your workers required to move heavy objects? Hand trucks and carts can help reduce the strain of lifting.
Whatever your company’s approach, the success of any safety initiative is dependent on the support of ownership and management. When someone identifies a threat to safety, prompt resolution of the issue — following previously-established policies or guidelines and driven by management — is important to maintain the strength and effectiveness of a risk management culture.
HARD TO DETECT, BUT WORTH IT
Solid procedures, employee screening, sound policies, and other risk management practices are essential. The tricky part is that the outcomes of a good risk management program are difficult to measure. When everything goes right, there aren’t any examples to prove the effectiveness of the efforts taken to minimize risk. There’s no paperwork, no accident site photos, no medical bills. But think about it: a chunk of your profits can disappear and morale can sink every time an employee slips, strains a muscle, falls, or fails to follow company policies and procedures. In this case, the absence of proof is the proof.
In a competitive business world, where turning a profit is often the highest priority, it’s tempting to sweep risk management under the rug with the expectation that an injury or accident won’t happen. That could be a costly mistake. Focus on risk management by creating and maintaining a culture centered on safety to bring business to the next level.
September 7, 2023